Parts Distribution Express (PDX)
Parts Distribution Express (PDX) is specifically designed to provide Komatsu subsidiaries and distributors with a robust and user-friendly platform for streamlining spare parts business. Offering a suite of exceptional features and functionalities, PDX empowers you to effortlessly manage daily and monthly operations associated with parts sales and purchases, while also keeping track of the status of parts being delivered to distributors or ordered from suppliers. Whether you are accessing the app through web portal or using our desktop version, PDX provides you the real-time, reliable data from anywhere, at any time.
Features
The PDX Web Portal is a one-stop-shop for Komatsu spare parts management, facilitating and expediting parts business among all stakeholders (Komatsu Ltd., subsidiaries and distributors). It offers a range of convenient functions, including real-time stock inquiries, quick and accurate order quotations, effortless conversion of quotes to sales orders, and customizable reporting tailored for specific distributors.
PDX's Sales Module consists of five key elements:
1: Quotation
2: Sales Order
3: Picking Packing
4: Shipping
5: Sales Invoice
The Quotation module allows distributors to request pricing information, which can be updated or changed before confirmation. By using Sales Order module we can registers confirmed distributor orders and allocate stock as per stock availability. Picking and Packing module manages the picking and packing of allocated stock from warehouses to prepare for shipment to distributors. Shipment module is used for dispatching goods to distributors with a cutoff dispatch time per order type. Sales Invoice module is used to issue invoices to distributors with the respective ordered parts, quantity of parts and payment due dates.
Each element of the Sales Module has sub-functions that work together seamlessly to ensure efficient sales management, enabling businesses to deliver their products to distributors quickly and efficiently.
PDX's Purchase Module provides a comprehensive solution for managing and tracking purchase orders, allowing subsidiaries to register orders with different suppliers. The module's core function Purchase Order Registration process enables subsidiaries to request parts, quantities, and agreed prices. Additionally, the Purchase Order module offers several sub-functions to complement the core functionality, including Purchase Order Inquiry, Purchase Order Condition, Purchase Order Detail, Purchase Order Status Inquiry, and PO Confirmations.
The Receiving section in PDX simplifies the process of receiving goods from suppliers by covering all activities involved, such as expense payable inquiry, expense registration, supplier invoice inquiry, supplier invoice condition, supplier invoice detail, binning instruction, and binning completion. These features make PDX's Purchase Module an efficient solution for managing all aspects of purchasing, from order placement to receipt of goods.
The Monthly Operations module is designed for subsidiary level users and includes processes that are essential for data integrity on a monthly basis. These processes include generating sales summary data, forecasting demand, predicting sales trends, setting up emergency stock, stock adjustment, and controlling stock parameters. The module ensures that the necessary monthly tasks are completed to maintain data accuracy and optimal stock levels and providing complete picture to higher management in the form of reports.
PDX offers a comprehensive solution for warehouse management, including support for all aspects of warehouse operations such as stock allocation, picking, packing, shipping, binning, and consignment stock handling. With PDX, you can easily configure and manage multiple warehouses, ensuring seamless operations across all locations. Whether you are dealing with a single warehouse or multiple facilities, PDX can help you optimize your warehouse operations and increase efficiency.
The consignment stock feature of PDX allows distributors to receive and store inventory for certain parts when there is high demand in their region. This helps reduce the number of orders from distributor and other related expenses. Distributors can easily register consignment sales invoices in PDX when they sell the consignment stock, streamlining the process of tracking and managing consignment inventory.
PDX utilizes historical ordering trends to forecast future demands, taking into account factors such as price ranking, order frequency, lead time, and safety stock. With a 12-month order history analysis, PDX provides Material Request Plan while streamlining the ordering process and minimizing the risk of overstocking or stockouts.
PDX's cross-docking feature is designed to handle back orders efficiently. Cross-docking is applied to specific distributor, end customers, order type, and commodity group. By using cross-docking, warehouses can reduce the time spent on operations by up to 45%, and overall shipment time by up to 20%. This results in faster delivery times for distributors and end customers.
The data archiving feature in PDX enables efficient management of transactional data by archiving data that is more than 3 years old (configurable). By optimizing the database for faster processing speeds, this feature ensures quick access to relevant data. The archived data can be easily accessed through various screens and reports, making it readily available for analysis and reporting purposes.
Streamlining & optimizing marketing campaigns and sales strategies, PDX offers Kitting feature that enables the sale of bundled packages. Collaborating with Komatsu Warehouse Management System, the application automates kit creation, making it easy to offer attractive discounts.
PDX offers a powerful reporting module that allows managers to generate reports from various aspects of parts operations. From daily order lists to sales trends, price hikes, and demand forecasting, PDX provides a comprehensive summary of critical data. Managers can analyze the information and optimize parts management strategies for better efficiency and profitability.
Benefits
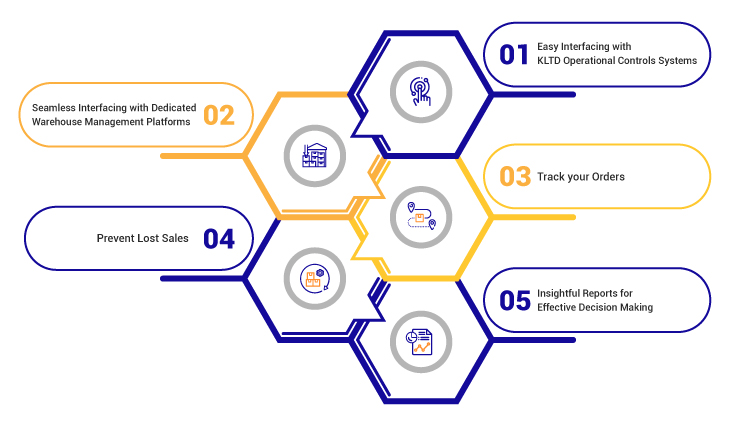
PDX goes beyond being just a user-friendly software solution, as it also offers the added benefit of easy interfacing with KLTD Operational Control Systems, ensuring seamless coordination between different aspects of your business operations. With PDX, you can efficiently integrate spare parts management with critical operations, helping you stay ahead of the competition and keep your business running smoothly.
In addition to interfacing with KLTD Operational Control Systems, PDX offers easy interfacing with dedicated warehouse management platforms, which means you do not have to change anything if you are already rendering the services of a warehouse management solution.
Monitor the progress of your orders from initiation to completion. Whether you're a distributor or a subsidiary, PDX offers a convenient interface to track your orders and stay informed of their status, whether they're initiated, in progress or already completed.
PDX empowers business users to detect and address lost sales opportunities. By providing a real-time overview of parts inquiries, availability status, and search trends, the system helps identify potential inventory shortages that lead to lost sales. With intelligent data analysis, PDX offers actionable insights and preventive measures to minimize future losses and ensure you stay ahead of customer demand.
The Reporting module empowers subsidiary level users to make informed decisions with a range of detailed reports. From documenting progress and comparing periods of time to providing a history of growth, these business reports deliver critical insights for better decision making. With the ability to track progress, control expenditures and increase revenue, management can leverage these reports to drive business success. The module includes a variety of reports, such as parts operation list, stock analysis list, sales order status reports, and many more, providing a comprehensive view of your business operations.